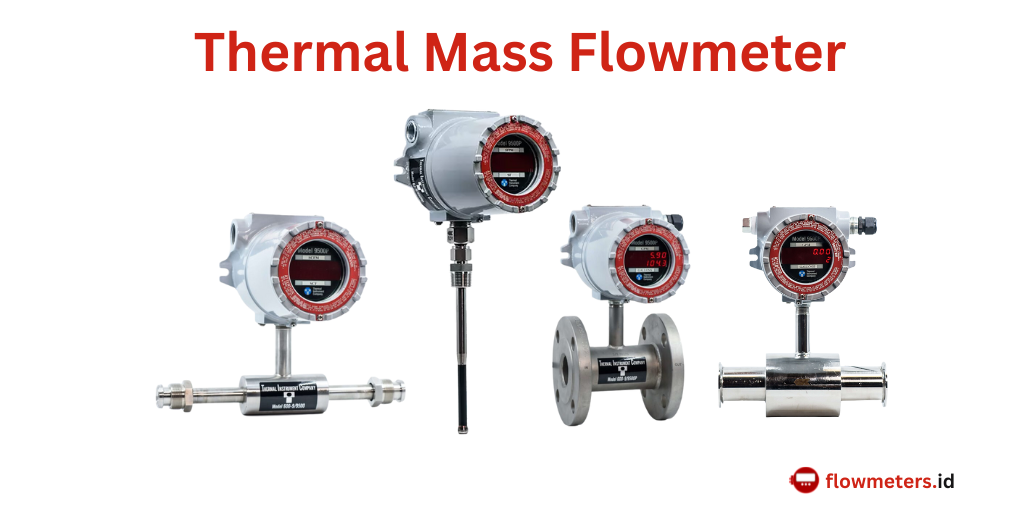
The Thermal Mass Probe Flowmeter accurately measures gas, liquid, or slurry flow rates in various applications. Unlike other models, our probe is designed with no clog-prone apertures, ensuring reliable performance. Enclosed in a sealed tube, our sensors can be easily inserted or removed during operation. We offer a mechanical retractor option if needed. Probes are crafted from durable materials like 316 SS, with options for corrosion-resistant alloys like Hastelloy C and Monel. Protective coatings such as Carbide, Fluorocarbon, Teflon, and Sulfinert enhance longevity and performance.
What is Thermal Mass Flowmeter and How does it operate?
Thermal Mass Flowmeters operate based on the principle of thermal dispersion, also known as the heat transfer principle. In this method, a heated sensor element is inserted into the fluid stream, and its temperature is maintained constant. As the fluid flows past the sensor, it carries away heat from the sensor. The rate at which heat is removed from the sensor is directly proportional to the mass flow rate of the fluid. This change in temperature is detected by one or more temperature sensors, usually thermistors or resistance temperature detectors (RTDs), located within the flow meter. By measuring this temperature change, the flow meter can accurately determine the mass flow rate of the fluid.
Imagine you’re making a cup of hot coffee on a chilly day.
As you pour milk from the container into your mug, you notice steam rising from the surface. The steam carries heat away from the milk, causing it to cool down slightly.
Similarly, in a thermal mass flowmeter, a sensor is heated to a constant temperature, and as fluid flows past it, it carries away heat, causing the sensor’s temperature to change. By measuring this temperature change, the flowmeter can tell how fast the fluid is flowing, just like you can gauge how quickly your milk is pouring by observing its temperature change.
A Wire Anemometer, or hot-wire anemometer, operates on the principle of convective heat transfer. The basic principle involves heating a wire to a constant temperature above the ambient temperature. As air flows over the wire, it cools the wire, causing its resistance to change. By measuring the change in resistance, the velocity of the airflow can be determined. This is achieved using an electrical circuit that monitors the resistance of the wire and converts it into a corresponding airflow velocity measurement.
How Wire Anemometer Works?
A wire anemometer typically consists of a thin wire made of a material with a high temperature coefficient of resistance, such as platinum. The wire is heated to a constant temperature above the ambient temperature using a small electrical current. As air flows over the wire, it cools the wire, causing its resistance to change. The change in resistance is measured using a Wheatstone bridge circuit or similar electronic circuitry. The airflow velocity is then calculated based on the known relationship between the wire resistance and the velocity of airflow.
Wire anemometers are commonly used in various applications, including meteorology, environmental monitoring, HVAC systems, and aerodynamics research.
These instruments are crucial in various fields such as environmental monitoring, HVAC systems, aerospace engineering, and industrial processes. Studying them helps students understand fundamental principles of fluid dynamics and heat transfer, applicable across numerous disciplines.
INSERTION PROBE THERMAL MASS FLOW METERS
Model 62-9
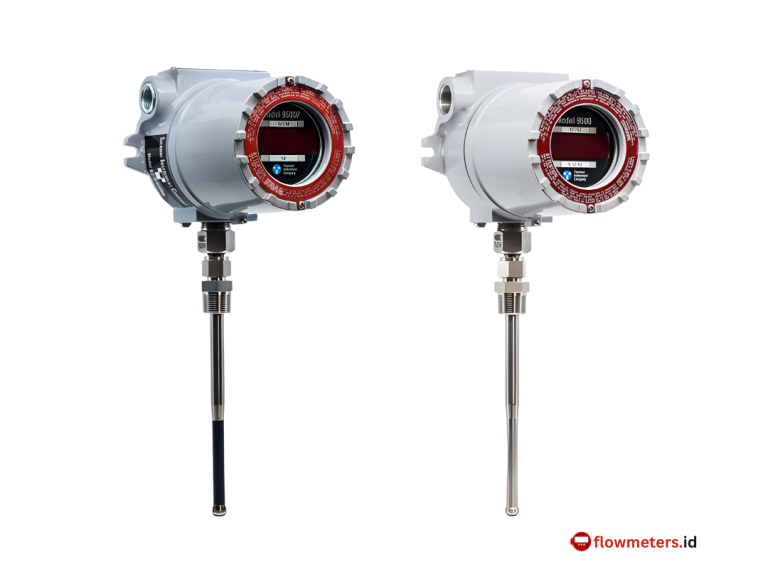
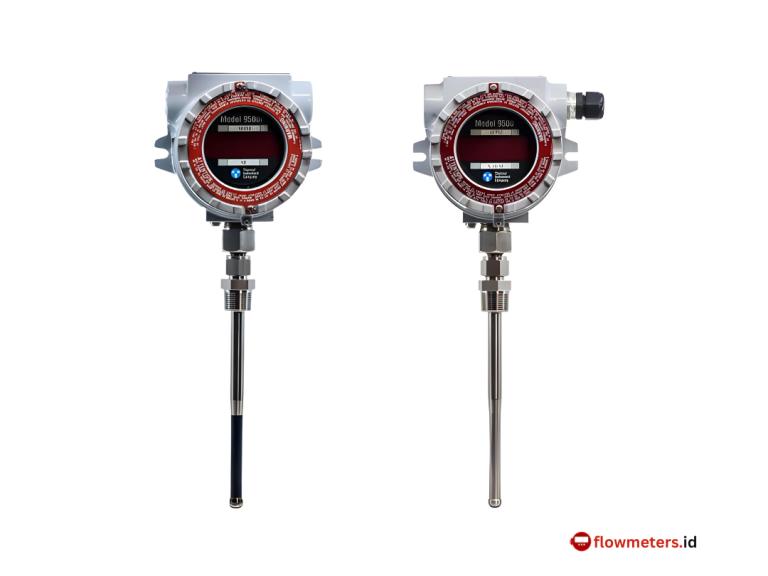
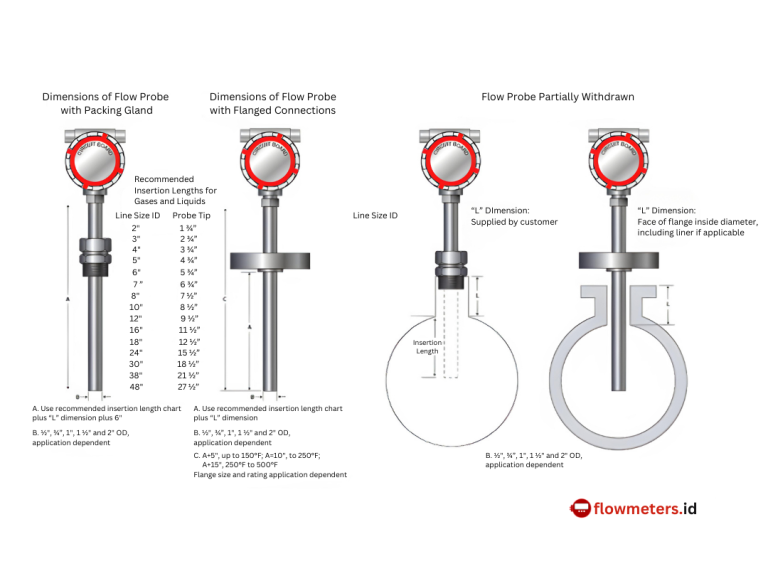
- Airflow Measurement for ducts and compressed air lines
- Natural Gas measurement to boiler
- Waterflow measurement for cooling operations
The Thermal Mass Probe Flowmeter is inserted directly into the flow stream to measure the flow rate of gases, liquids, or slurries in piping, irregularly shaped lines, and process ducts. Unlike other probe flow meters, we offer a model that has no apertures that can be clogged with particles or distorted by wear. Our sensors are enclosed in a sealed tube which can be inserted or removed through a gate valve or a packing gland while conduit is in use.
We also offer a mechanical retractor if required for your application. Our probes are manufactured using 316 SS as a standard, but corrosion resistant materials such as Hastelloy C, Monel, Inconel, Tantalum, and Carpenter 20 are also available. In addition, our Thermal Mass Flow Meters are available in a variety of protective coatings including Carbide, Fluorocarbon, Teflon, and Sulfinert.
APPLICATIONS:
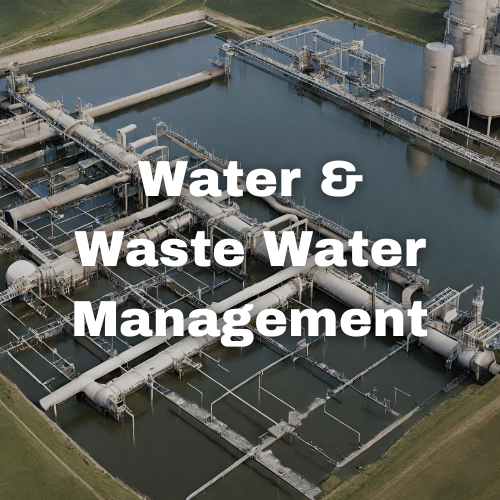
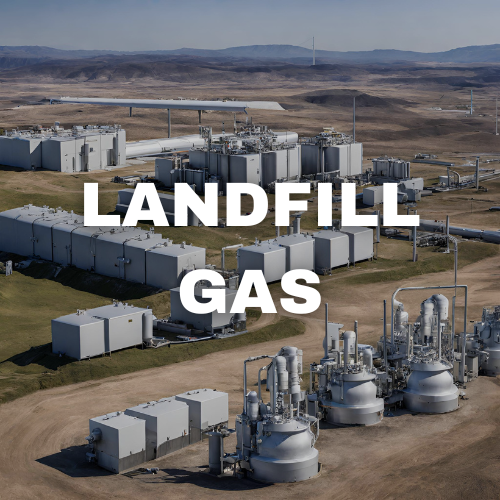
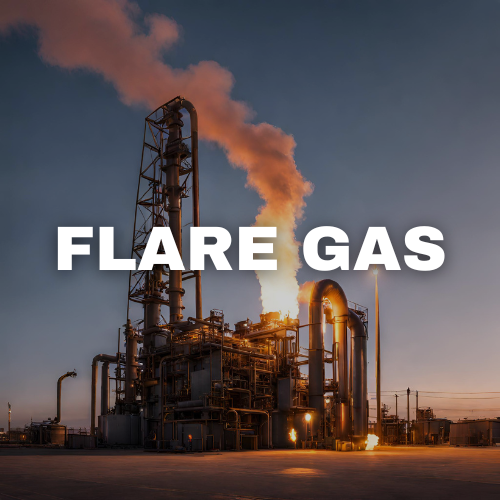
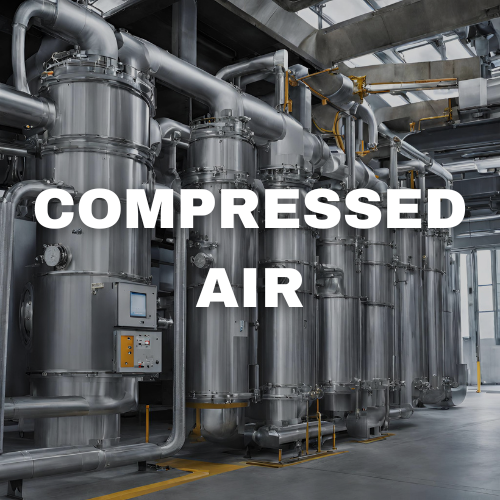
INLINE THERMAL MASS FLOW METERS
Model 600-9SAN
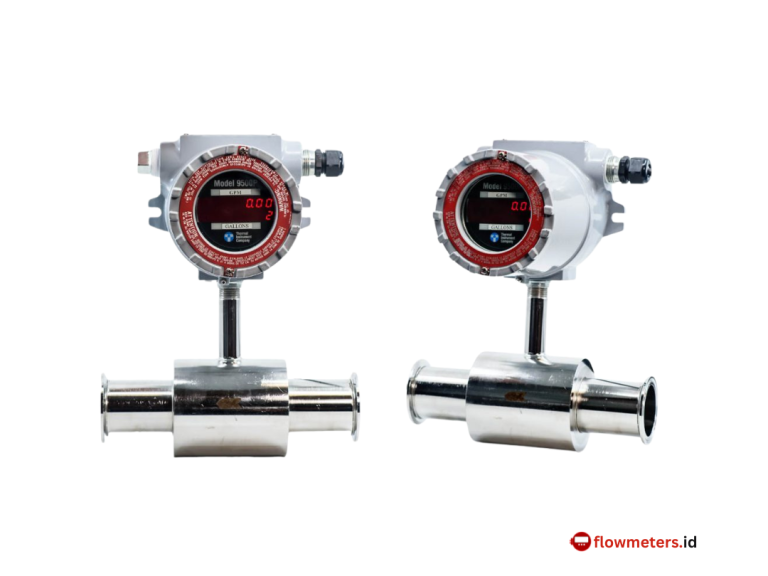
- Food & Beverage Applications
- Pharmaceutical CIP Applications
- Available in a wide variety of OD sizes
- 316L SS Standard Material of construction
- 15Ra Flow Wetted Surface finish
- 3A Sanitary Approval
- Flow sensors can hold up to the demands of “CIP” conditions
Thermal Instrument offers diverse flow meters tailored to clients’ needs. Our Model# 600-9 SAN flow sensor mirrors the benefits of our #600-9, catering to sanitary process conditions. Crafted from 316L SS with a 15 Ra flow wetted surface finish, it ensures durability.
Featuring tri-clamp and tube end connections, each unit includes redundant Flow and Temperature RTD sensors. Delivering 4-20 mA outputs for flow and temperature information, our sensors are calibrated for various liquids and gases, including those in food, beverage, and pharmaceutical industries.
We specialize in fuel and water flow meters, calibrated for air, carbon dioxide, DI water, food additives, dairy products, and more.
APPLICATIONS:
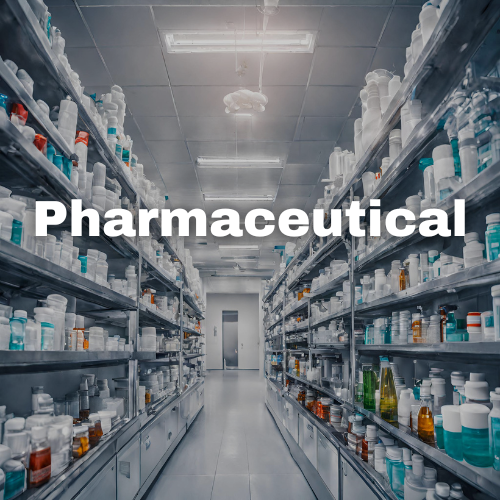
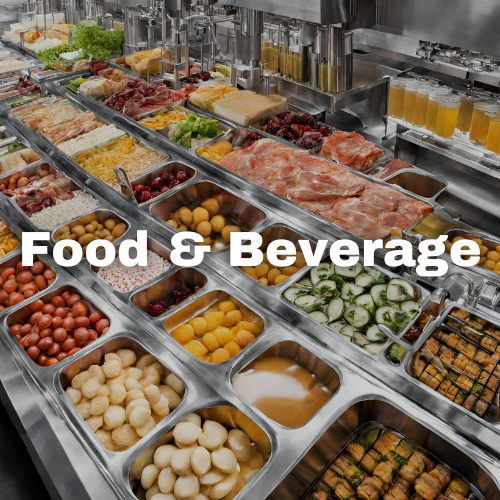
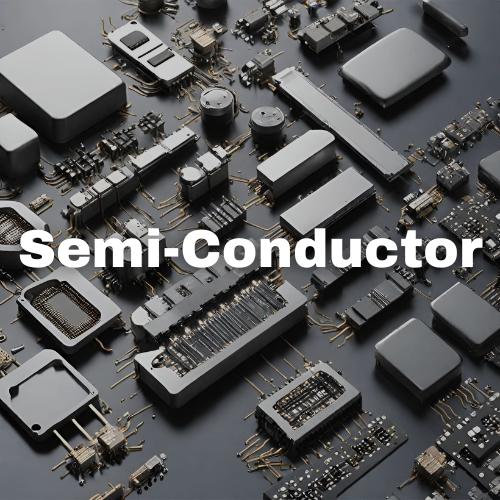
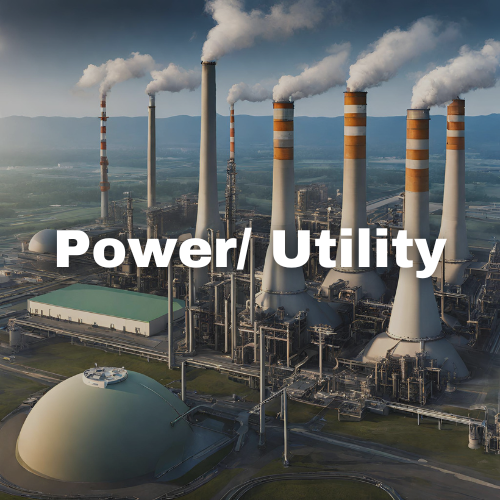
Model 600-9
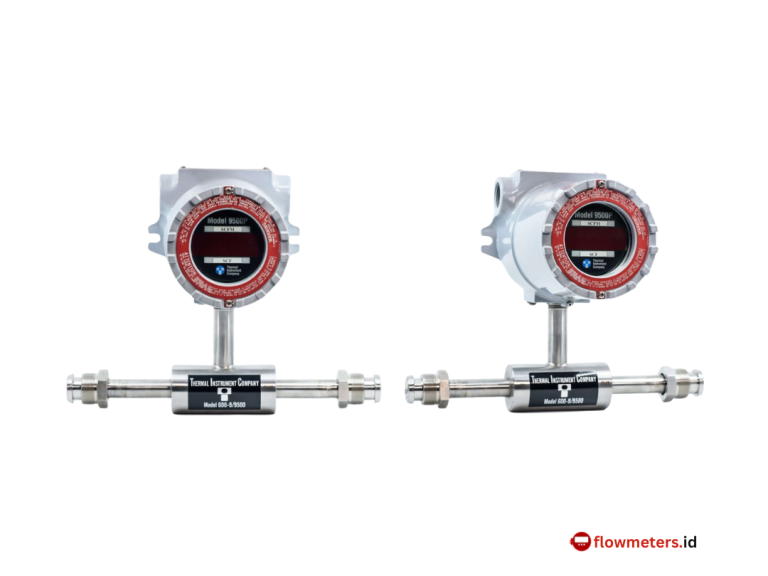
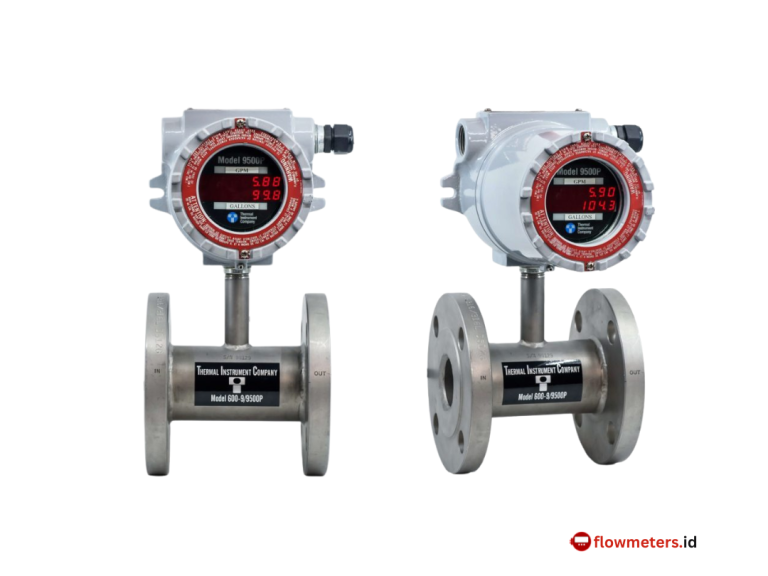
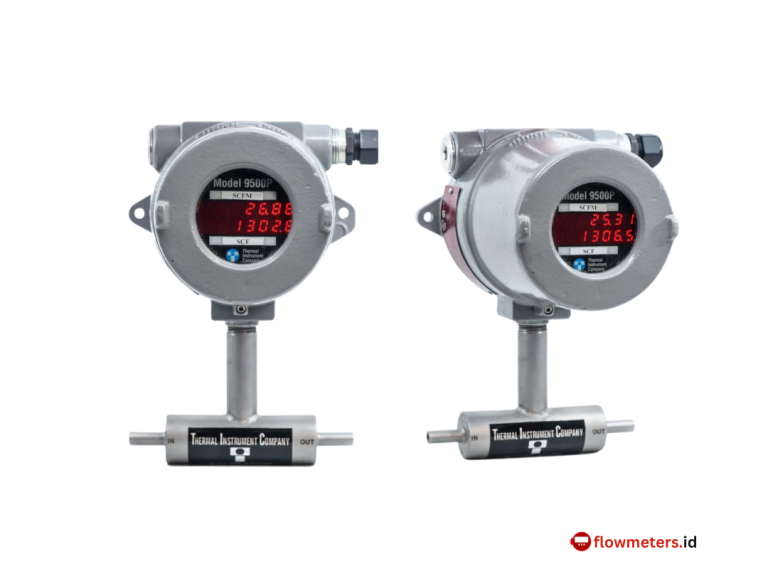
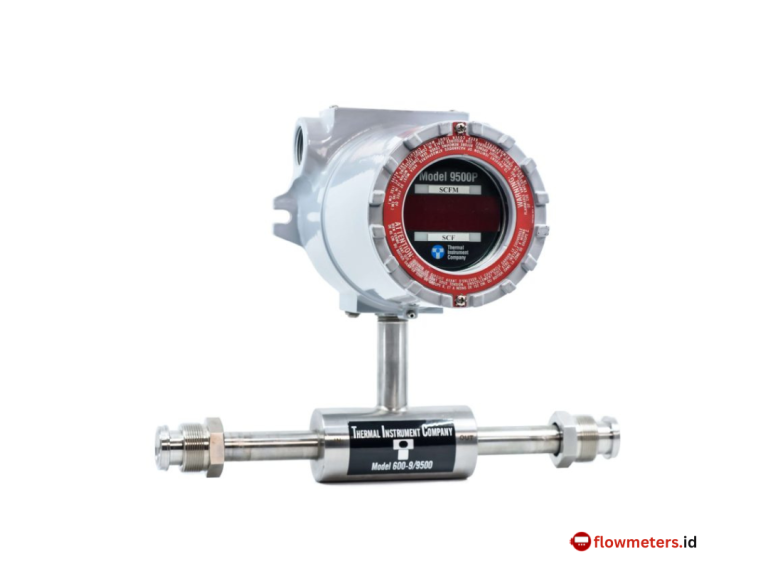
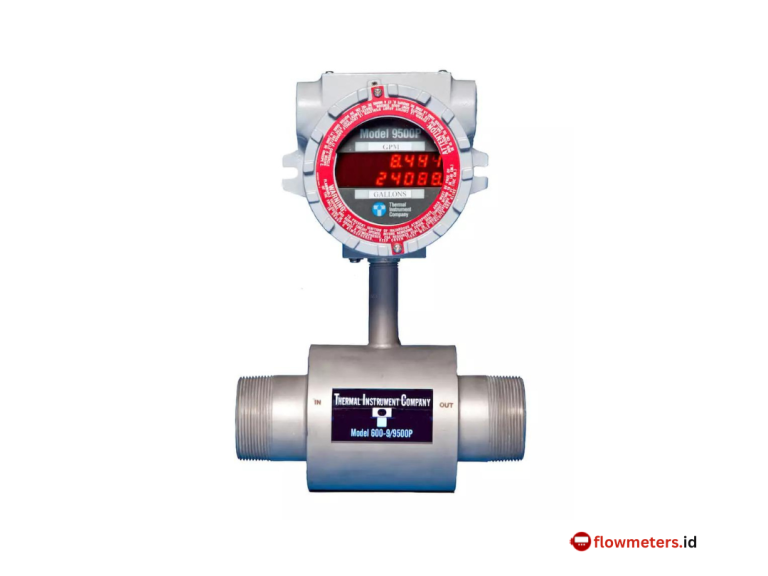
Thermal Instrument pioneered the development of in-line flow meters, boasting a unique design that ensures the flow and temperature sensor remain shielded from passing fluids at all times. Our exclusive in-line gas flow meters and liquid flow meters guarantee exceptional accuracy and repeatability, instilling confidence in our clients. With the versatile 600-9 model, we offer a wide range of process connections for swift installation, catering to demanding flow applications.
Our mass flow sensors feature redundant Flow and Temperature RTD sensors, ensuring longevity and maximizing return on investment. Stay informed about your flow meters’ status with the 600-9 flow sensor, providing crucial flow and temperature data via a 4-20mA output connection.
The Model#600-9 boasts an unobstructed flow path adaptable to line sizes ranging from ¼” to 12”, minimizing pressure drop and enhancing operational efficiency. Customizable to fit specific requirements, our flow sensors are constructed with robust materials like Hastelloy-C, Tantalum, Titanium, Monel, and more, ensuring durability even in corrosive environments.
The Model#600-9 can be customized for corrosive or demanding applications. We offer various connection options, including flange connections, NPT sizes, and adaptable tube ends. Additionally, protective coatings can be applied to wetted surfaces, providing enhanced corrosive protection and peace of mind in challenging environments.
- Variety of Connections Available
- Unobstructed Flow Path
- Negligible Pressure Drop
- Highly Accurate – ± 1% Accuracy across Full Scale in most applications
- Repeatable Rates – ± 2%
- 100:1 Turndown or better on most applications
- Small Line sizes down to ¼”
- Large Line sizes up to 12”
- Capable of providing Flow and Temperature details across independent 4-20mA outputs
- Numerous Process Connections Available – Flange, NPT, Tube Ends, etc.
- Redundant Sensors
- Protective Coatings Available
- Exotic materials including Tantalum, Hastelloy-C, Titanium, and Monel
- Long Life = Return on Investment
- Available in Sanitary & Ultra High Pure Finishes
- Great for air & gas measurement
- Great for water & other liquid measurement
APPLICATIONS:
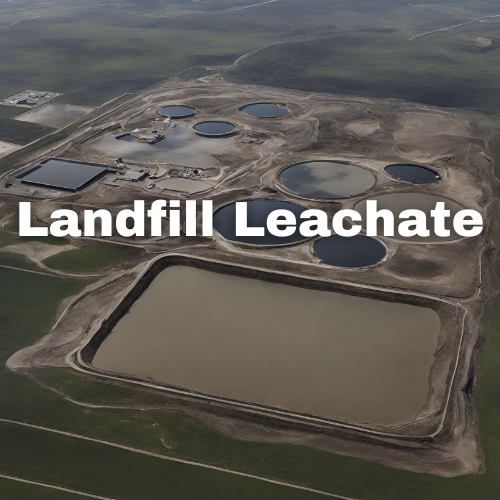
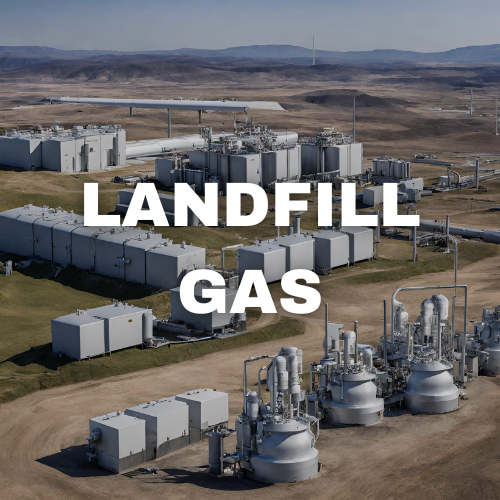
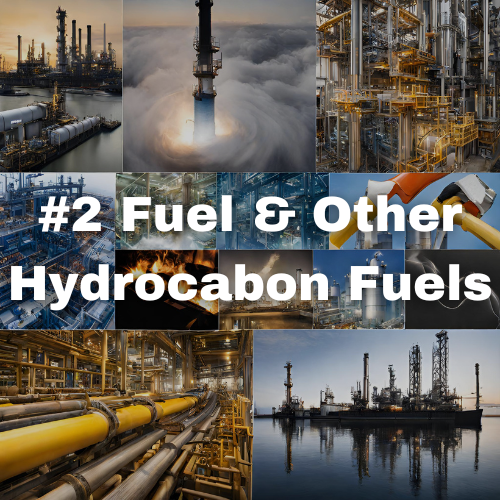
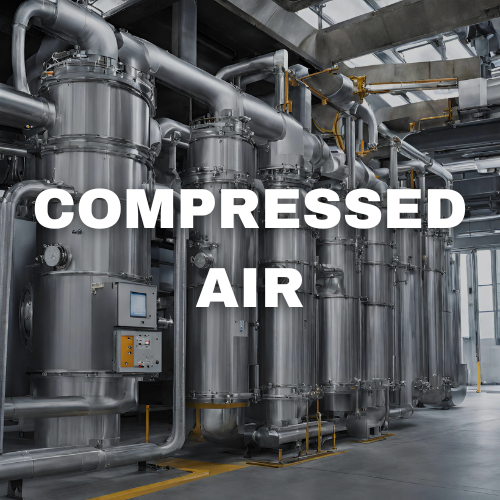
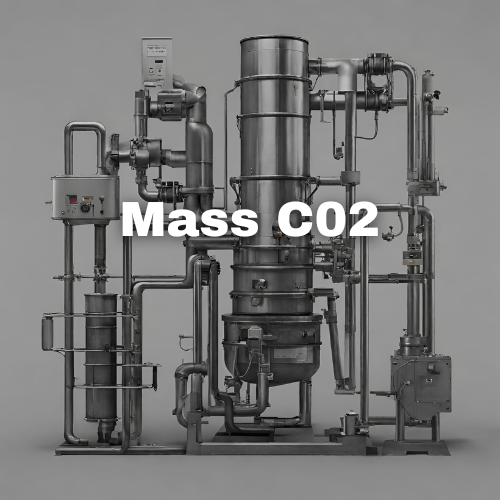
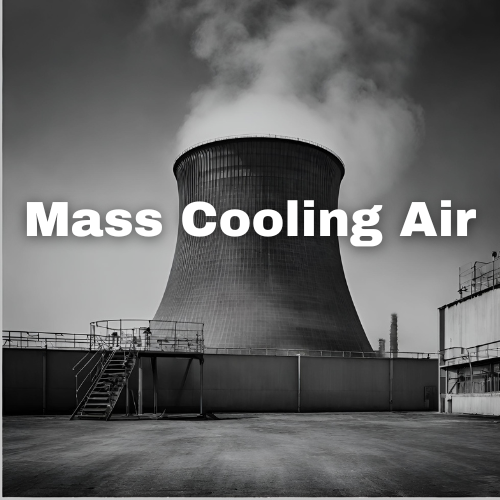
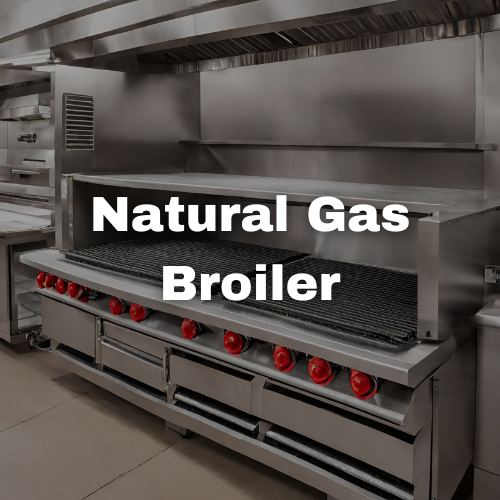
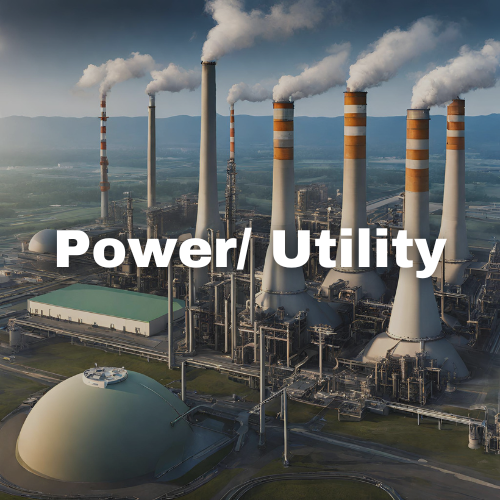
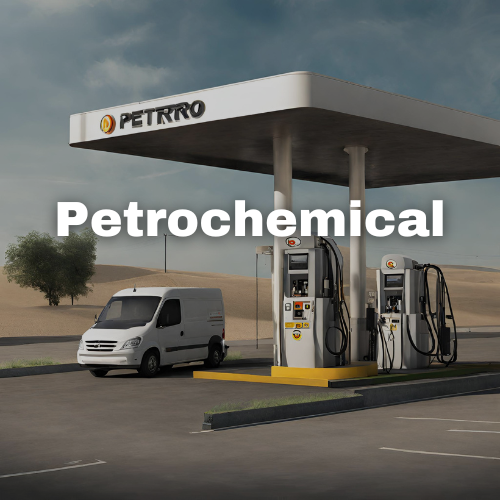
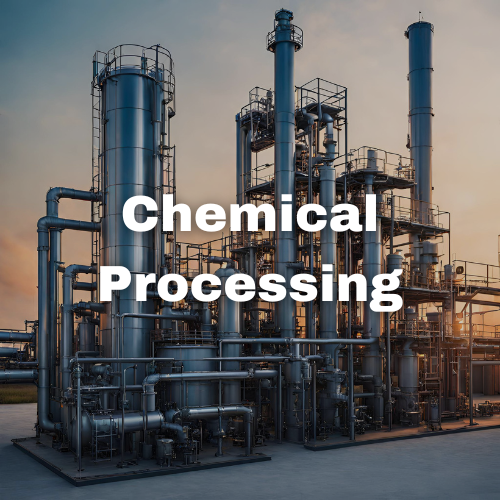
Related products:
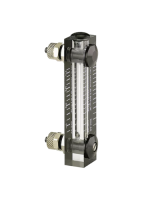
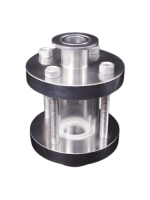
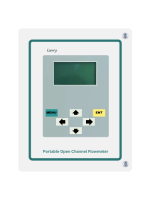
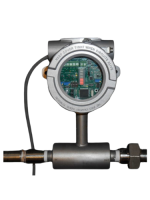
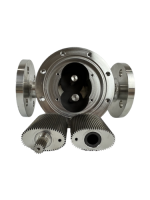
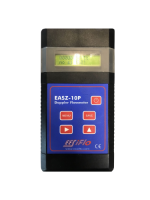
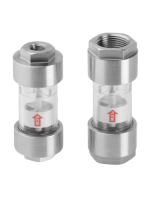
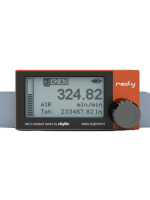
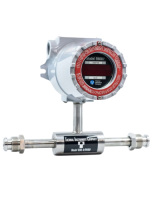
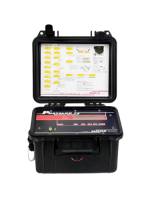
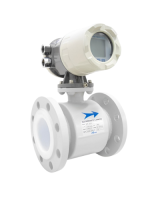
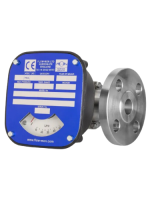