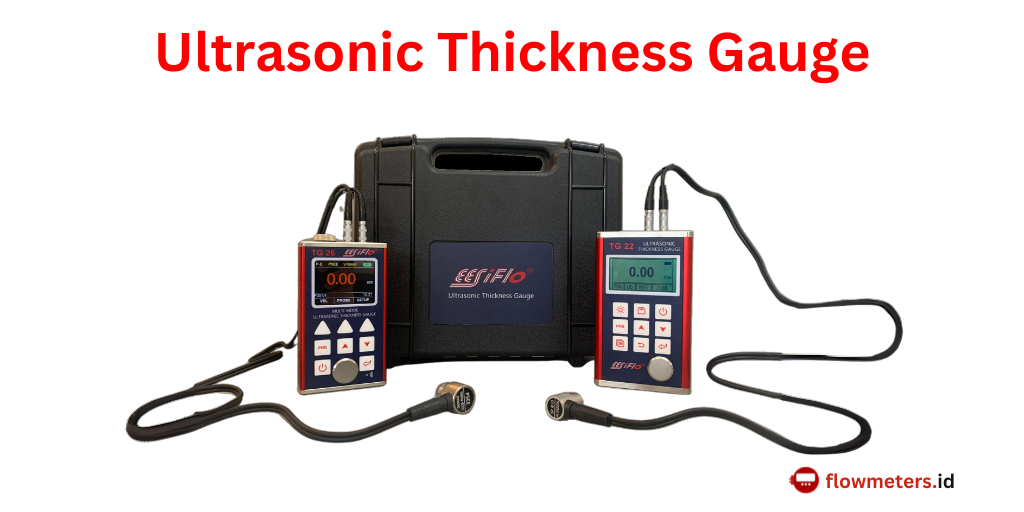
Understanding the Ultrasonic Thickness Gauge: A Quiet Revolution in Measurement
In the world of materials and machinery, where steel meets pressure and pipelines span continents, understanding the integrity of those materials isn’t just helpful—it’s essential. This is where the ultrasonic thickness gauge steps in, a marvel of modern engineering that allows technicians and engineers to “see” inside solid objects without leaving a scratch.
At first glance, the device appears modest—handheld, compact, and unassuming. But beneath its simple exterior lies a precise instrument that uses the power of sound, much like how a bat navigates in darkness or how sonar scans the depths of the ocean. The principle is elegant: a small probe sends out a burst of high-frequency sound waves into the material. These waves travel through the object and bounce back upon reaching the opposite surface. By measuring the time it takes for the echo to return, the device calculates the thickness of the material with remarkable accuracy.
This technique, known as ultrasonic testing, has revolutionized how industries maintain safety and efficiency. Whether inspecting the thinning walls of an aging pipeline, ensuring the structural integrity of an aircraft fuselage, or verifying the uniformity of a plastic mold, the ultrasonic thickness gauge provides critical insight—without cutting, drilling, or dismantling a single part.
Used across industries—from shipbuilding and oil refineries to aerospace and civil engineering—this tool ensures that what’s invisible to the eye doesn’t remain unknown. It’s a silent sentinel of safety, catching wear and corrosion before they become catastrophic failures.
In essence, the ultrasonic thickness gauge is more than a measurement tool—it’s a guardian of structure, a whisperer of walls, and a testament to the quiet genius of sound.
TG 22- Ultrasonic Thickness Gauge
The TG22 is a precision digital thickness
gauge based on ultrasonic measurement principles. Designed for versatility, it
accurately measures the thickness of a wide range of ultrasonic-conductive
materials, including metal, plastic, ceramic, glass, and more.
In addition to standard thickness measurement, the TG22
features an alternative velocity measurement mode, allowing users
to determine the specific sound velocity of various materials. This makes it
ideal for customized testing and calibration on different substrates.
Unlike traditional thickness measurement methods, the TG22
offers a non-destructive and highly efficient solution. It
requires access to only one side of the workpiece, enabling
accurate measurements without interrupting ongoing processes or operations. To
operate, simply apply the acoustic coupling compound to the probe, press it
firmly against the material surface, and the device instantly provides a
reliable thickness reading.
The instrument also supports onboard data storage,
allowing thickness readings to be saved directly in the device for convenient
retrieval and analysis later.
Thanks to its advanced performance and user-friendly design,
the TG22 is the ideal tool for inspecting closed pipes, containers,
pressure vessels, and more. It is widely used across a variety of
industries—including petroleum, chemical processing, metallurgy,
shipbuilding, aviation, and aerospace—for quality control,
production monitoring, and routine inspection tasks.
- Large
back lit LCD Display - Rugged
Hand-held design - Zero
point calibration, two-point calibration, automatic error correction
system - Coupling
status indicator - Auto
Sleep and auto power off function to conserve battery life - Small,
portable, high reliability for harsh operating environment, anti-
vibration, antishock and anti-electromagnetic interference
- Pipelines
- Storage
tanks - Lighting
Columns - Road
Tankers - Bridges
- Pressure
Vessel
EESIFLO: TG22
Design: Field instrument with 1 measuring channel
Transducers: EES-N05/90⁰ (Standard Supply)
MEASUREMENT
Measurement Principle: Transit time difference correlation principle (pulse/echo)
Measuring Range: mm 0.75…300 (in steel)
Sound Velocity: m/s 300…19999
Resolution: mm 0.1 / 0.01
Measurement Frequency: Single-point measurement 4/s, Scan Mode 10/s
Accuracy: ± 0.5% of reading ( ± 0.01mm thickness)
TRANSMITTER
Power Supply: Two “AA” Size, 1.5 volt alkaline batteries
Memory Capacity: Memory for 100 files (up to 100 values for each file) of stored values
Alarm Function: Upper and lower limit can pre-set.
*It alarms automatically when the result value exceeding the limit
Working Time: 100 hours typical operating time (EL backlight off)
Housing Material: Extruded aluminium body suitable for use under harsh environment
Dimension: mm 130 x 76 x 32
Weight: g 345
Ambient Temperature: ⁰C -10…+50
Display: 4.5 digit LCD with EL backlight
Menu Language English, German, French, Spanish, Italian
COMMUNICATION (OPTIONAL)
Interfaces: USB 2.0
TG 26- Ultrasonic Thickness Gauge
The TG26 Digital Thickness Gauge is a robust, hand-held instrument designed for accurate thickness measurement of various materials such as metals, plastics, ceramics, and glass. It includes a TFT color display, multi-mode operation (Pulse-Echo and Echo-Echo), and Bluetooth wireless capability. The device allows for measurements without removing paint or coatings and includes calibration functions, a coupling status indicator, and power-saving features. It is suitable for harsh environments with its anti-vibration, anti-shock, and anti-electromagnetic interference design. The TG22 also supports USB 2.0 communication and comes in a durable extruded aluminum body. This versatile gauge is ideal for applications including pipelines, storage tanks, lighting columns, road tankers, bridges, and pressure vessels.
- TFT Colour Display
- Multi-Mode Pulse-Echo, Echo-Echo
- Echo-Echo Mode perform measurement without removing the paint or coating
- Rugged Hand-held design
- Zero point calibration, two-point calibration, automatic error correction system
- Coupling status indicator
- Auto Sleep and auto power off function to conserve battery life
- Small, portable, high reliability for harsh operating environment, anti- vibration, anti-shock and anti-electromagnetic interference
- Integrate with Bluetooth wireless capability
- Pipelines
- Storage tanks
- Lighting Columns
- Road Tankers
- Bridges
- Pressure Vessel
- Multi-Mode: Pulse-Echo mode and Echo-Echo mode.
- Capable of performing measurements on wide range of material,
- including metals, plastic, ceramics, composites, epoxies, glass, and other ultrasonic
- wave well- conductive materials.
- Special transducers models are available for special applications, including for coarse
- grain material and high temperature applications.
- Probe-Zero functions, Sound-Velocity-Calibration fuction
- Two Point Calibration fuction.
- Three Working modes: normal mode, scan mode and diff mode.
- Coupling status indicator showing the coupling status.
- Units: Metric or Imperial unit selectable.
- Battery information indicates the rest capacity of the battery.
- Auto sleep and auto power off functions to conserve battery life.
- USB2.0 Communication Port
- Bluetooth Support
- Size: 120mm x 67mm x 31mm
- Weight: 295 g
Measuring Principle
The digital ultrasonic thickness gauge determines the
thickness of a part or structure by accurately measuring the time required for
a short ultrasonic pulse generated by a transducer to travel through the
thickness of the workpiece, and the sound waves are coupled into the test
material and travel through it until they encounter a back wall or other
boundaries. The reflections then travel back to the transducer, which converts
the sound energy back into electrical energy. In essence, the gauge listens for
the echo from the opposite side. Typically this time interval is only a few
millionths of a second. The gauge programmed with the speed of sound in the
test material, from which it can then calculate thickness using the simple
mathematical relationship.
Note: To make sure the gauge working properly, it needs to use coupling compound to fill the gaps between the transducers surface and the measured workpiece surface.
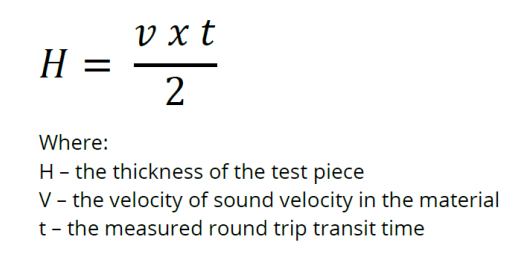
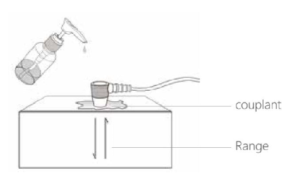
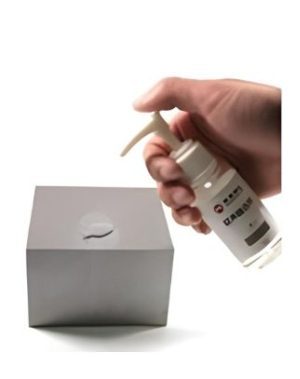
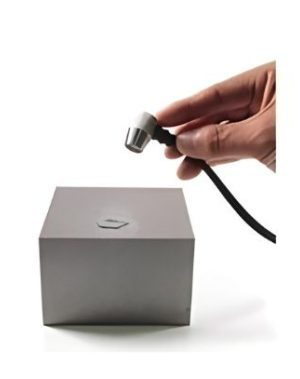
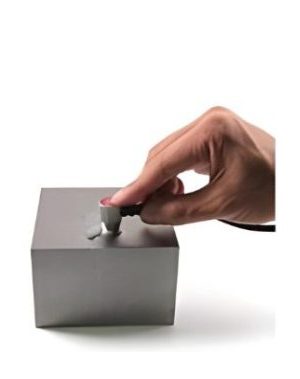
Optional Spare Transducer Selection
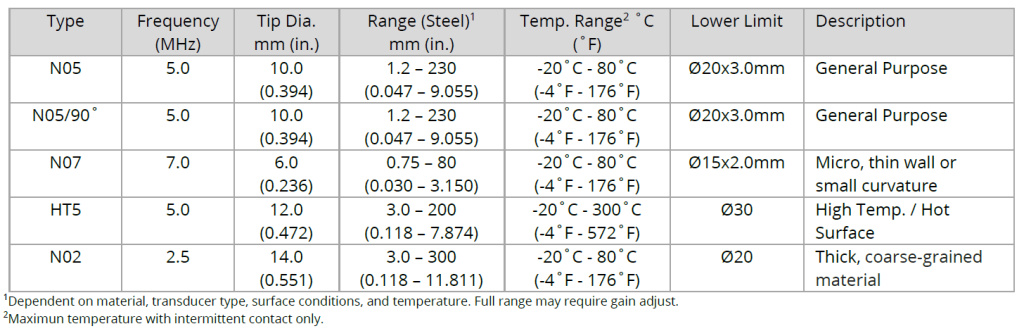